Norske Eskil (34) jobber på et av verdens mest spesielle skip
Aldrende oljeinstallasjoner og nye offshore vindparker har skapt grobunn for en helt spesiell type fartøy.
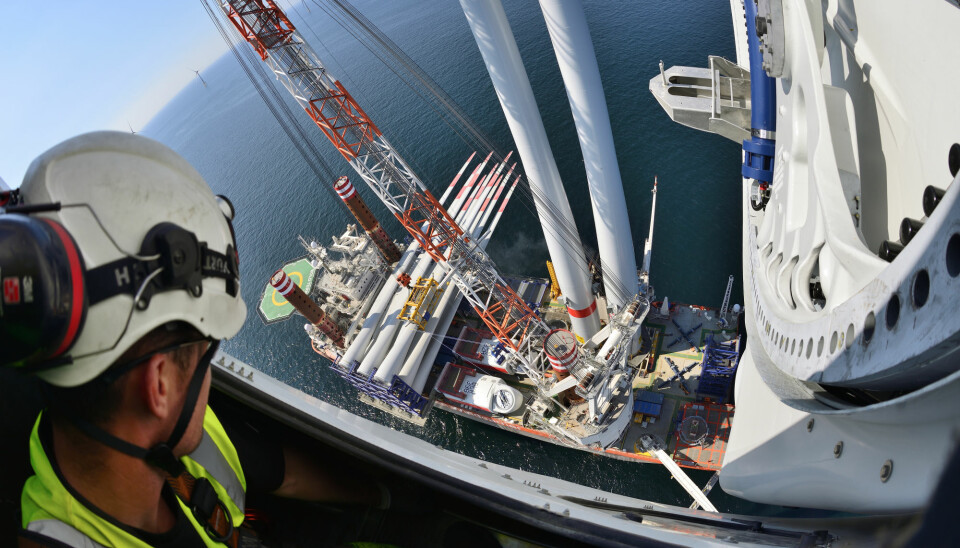
En offshorerigg står med fire ben godt plantet på havbunnen i Nordsjøen. Den er hyret inn i forbindelse med byggingen av en offshore vindpark. Oppdraget er å plasser flere tonn tunge fundamenter på havbunnen, 50–79 meter under havoverflaten. Deretter blir de opptil 120 meter høye turbinene løftet på plass. Så langt er alt normalt.
Når jobben er gjort, vindmølleparken klargjort og riggen skal videre til neste oppdrag, blir skroget på riggen jekket ned til havoverflaten og bena jekket opp fra havbunnen.
LES OGSÅ: Ny teori om Alexander den store: Lå levende død i seks dager
Jackup-rigger har eksistert siden den første kom i 1954. Vanligvis har de vært avhengig av slepebåter. Men nå finnes det rigger som ikke er avhengige av slepebåter. De seiler for egen maskin.

Fred. Olsen-skip

Som fartøyene «Bold Tern» og «Brave Tern». De trenger ingen form for assistanse fra slepebåter, men er helt selvdrevne. De kan både losse, laste, transportere, installere, innkvartere og frakte seg selv til og fra oppdragene. Begge inngår i porteføljen til Fred. Olsen Windcarrier.
Begge skipene er 132 meter lange, 39 meter brede og har et dekkareal på 3200 kvadratmeter. Bena er 92 meter lange og skipene kan operere på 50–60 meters dyp. Dybden er ulempen med løftefartøyene sammenlignet med en tradisjonell jekkerigg, men vindparker blir som regel installert på dyp hvor løftefartøyenes kapasitet er tilstrekkelig. Windcarrier-fartøyene er utstyrt med helikopterplattform og hovedkranen om bord kan løfte 800 tonn. Opptil 80 personer kan innkvarteres fordelt på 56 rom som alle er utstyrt med dusj, toalett og satellitt-tv. Mannskapet har tilgang på blant annet treningsrom om bord.
LES OGSÅ: Brukt bobil - slik gjør du et trygt bruktkjøp

Begge skipene er bygget ved Lamprell-verftet i Emiratene og begge er utstyrt med dynamisk posisjoneringssystem (DP2) fra Kongsberg Maritime. Dynamisk posisjonering en metode for å holde skip og halvt nedsenkbare plattformer i samme posisjon over havbunnen uten bruk av anker, men ved hjelp av fartøyets egne propeller. DP krever en egen datamaskin som samler data om bølgenes virkning på skroget, om vind, hvilken retning fartøyet peker i, og nåværende posisjon.

Ledet av nordmann
I august var «Bold Tern» hyret til å installere turbiner tilknyttet vindparken Borkum Riffgrund 2 som ligger 57 kilometer utenfor kysten av Tyskland.
Parken har de kraftigste turbinene på tysk sokkel. Hver av de enorme 8,3 Megawatt-turbinene rager 109 meter over havet opp til de såkalte nacellene med generatoren. Fra havoverflaten til vingetuppen er det rundt 190 meter.
De gigantiske vingene har et vingespenn på 164 meter, og vindparken på Borkum Riffgrund vil generere energi til om lag 460 000 tyske husstander.
LES OGSÅ: Test av Osprey Hikelite 26 - enkel og solid dagstursekk
Prosjektleder for oppdraget til «Bold Tern» var nordmannen Eskil Røset som jobber i Fred. Olsen Windcarrier.
– Vi bruker fra 12 til 18 måneder på å forberede en slik operasjon. Vi planlegger ned til minste detalj slik at oppdraget på feltet skal gå så sømløst som mulig. Målet var å bruke maks ett døgn per turbin, men vi lyktes med å gjennomføre oppdraget på enda kortere tid enn estimert, forteller Røset.
Vindparkene er naturlig nok plassert på steder som er utsatt for vind, men vinden kan også være den største utfordringen ved installering. Likevel skal det mye vind til før skipene må ligge i ro.
– Tårnene utfører tunge og ganske stabile løft, så vi kan jobbe under forhold med opptil 14 sekundmeter i snitt, og vindkast på 17,5 m/s, forteller Røset. 14 meter per sekund tilsvarer liten kuling.
– Vingene er konstruert for å fange vind, så de er noe mer sårbare. Men vi greier å installere i 12 sekundmeter i snitt, og vindkast opptil 15 m/s. Uansett vær så skal slike tunge løft behandles med respekt. Går det først galt, kan det gå fryktelig galt, sier Røset.
På Borkum Riffgrund 2 var også flere norske selskaper involvert som Norges Geotekniske Institutt og Framo.

USAs første vindpark
Han var også prosjektleder for USAs første offshore vindmøllepark, Block Island Wind Farm, som ble installert utenfor Rhode Island i 2016. Den gangen var det «Brave Tern» som var i aksjon og det tok skipet 15 døgn å seile over Atlanteren. Siden skipet måtte frakte komponenter til vindparken fra Europa og USA, bød det på ekstra utfordringer.
– Skipene er robuste og tåler fint en slik overfart, men de er ikke optimalisert for det. Det er jo ikke rare fribordene å snakke om, så vi måtte beskytte lasten mot sjø på dekk, sier Røset.
Nacellene på turbinene består av blant annet generatorene og sårbar elektronikk, og for å sikre komponentene mot sjø ble de plassert fem meter høyere på dekk enn normalt. Dersom bølgene skulle slå over dekk, ville de dermed skylle under de sårbare nacellene.

Det største i klassen
Det er det danske selskap Ørsted som eier deler av Borkum Riffground 2. Av de 59 turbinene på feltet er 20 såkalt bøttefundamenterte. (se undersak). Hvert fundament er 58 meter høyt og veier 950 tonn. Til dette arbeidet ble verdens største løftefartøy benyttet, GeoSeas 147,5 meter lange «Innovation».
Det har et dekkareal på 3400 kvadratmeter og er spesiallaget for å håndtere vindturbiner med en lengde på opptil 120 meter. Bena som brukes til å fundamentere skipet på havbunnen, er 89 meter lange.
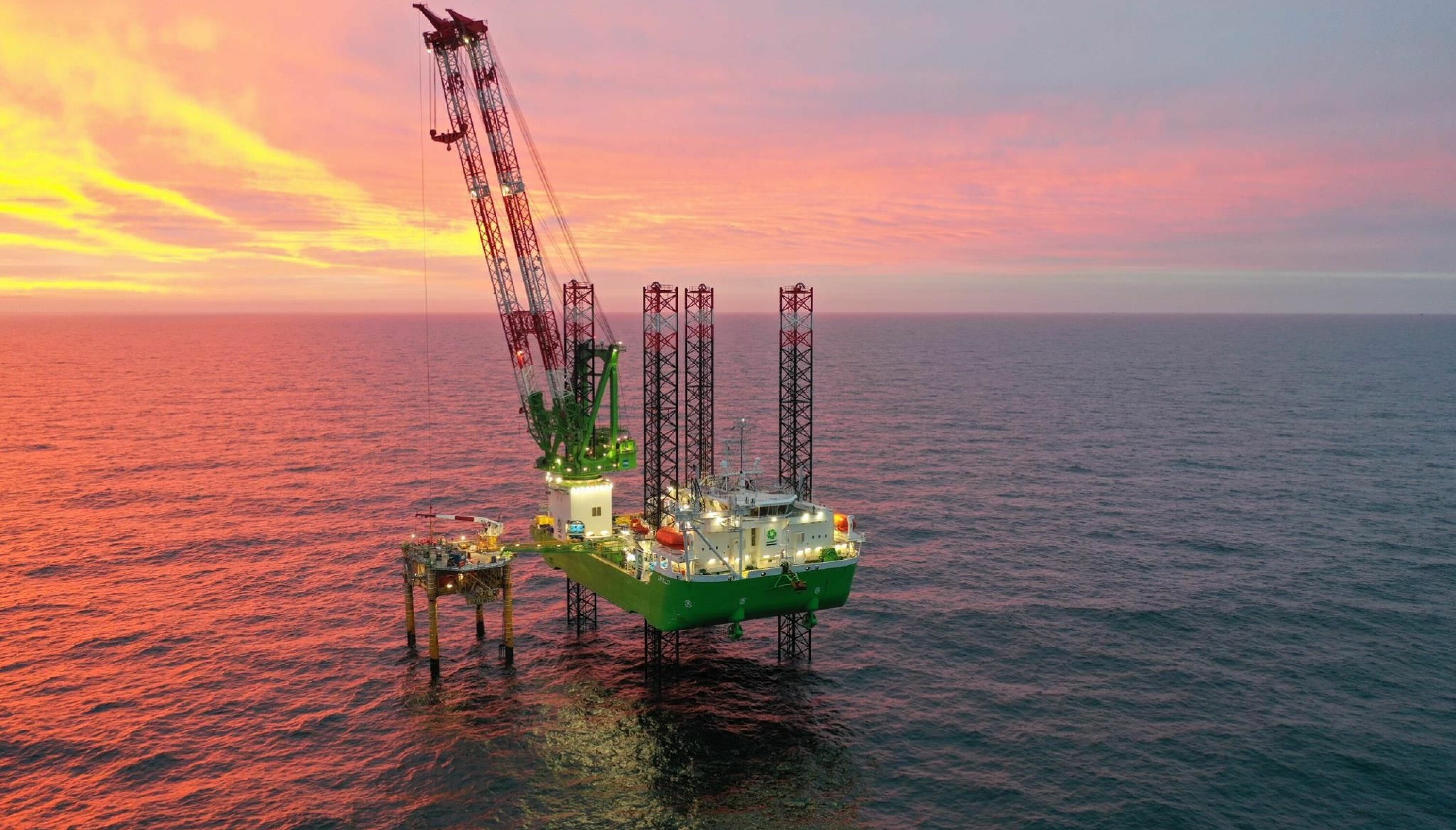
Nytt rekordfartøy
Nylig sjøsatte GeoSeas ytterligere et spektakulært løftefartøy. «Apollo» er den siste og råeste tilveksten til flåten av disse selvdrevne jackup-riggene som fra før teller nevnte «Innovation», samt «Neptune», «Thor», «Sea Installer» og «Sea Challenger».
«Apollo» er utstyrt med fire 106,8 meter lange ben som gjør at fartøyet kan jobbe på 70 meters dybde. Først den 9. august i år sto det ferdig ved verftet Uljanik i Pula i Kroatia. Derfra seilte det umiddelbart fra Adriaterhavet til Vlissingen i Nederland for de siste klargjøringene til sitt første oppdrag. Også «Apollo» er utstyrt Kongsberg DP2.
Like etter ble det sendt til den nederlandske sektoren av Nordsjøen for å starte demonteringen av den ubemannede gassplattformen Q1 Halfweg som ble reist i 1995. Av de 150 plattformene som står i nederlandsk sektor skal 77 fjernes innen 2025.
Kilder: Fred. Olsen Windcarrier, Deme-Group, NGI og Wikipedia